Porosity in Welding: Identifying Common Issues and Implementing Ideal Practices for Prevention
Porosity in welding is a prevalent problem that typically goes undetected till it triggers significant troubles with the stability of welds. In this discussion, we will discover the essential variables contributing to porosity formation, analyze its damaging impacts on weld efficiency, and discuss the finest techniques that can be embraced to minimize porosity occurrence in welding processes.
Typical Reasons of Porosity

Another regular perpetrator behind porosity is the visibility of contaminants on the surface area of the base metal, such as oil, oil, or corrosion. When these contaminants are not successfully gotten rid of prior to welding, they can evaporate and become trapped in the weld, triggering problems. Moreover, utilizing filthy or wet filler materials can present contaminations right into the weld, contributing to porosity issues. To mitigate these typical sources of porosity, detailed cleansing of base metals, appropriate securing gas option, and adherence to optimum welding specifications are vital practices in attaining top quality, porosity-free welds.
Effect of Porosity on Weld Quality

The existence of porosity in welding can dramatically compromise the architectural integrity and mechanical residential or commercial properties of bonded joints. Porosity develops gaps within the weld metal, deteriorating its overall stamina and load-bearing ability.
Welds with high porosity levels tend to show reduced influence stamina and minimized ability to deform plastically prior to fracturing. Porosity can impede the weld's ability to effectively transfer pressures, leading to premature weld failure and possible safety risks in browse this site vital frameworks.
Finest Practices for Porosity Avoidance
To improve the architectural integrity and quality of welded joints, what specific measures can be applied to lessen the incident of porosity during the welding process? Making use of the correct welding technique for the details material being bonded, such as changing the welding angle and weapon setting, can even more protect against porosity. Normal evaluation of welds and immediate removal of any type of issues determined throughout the welding process are crucial practices to protect against porosity and generate top notch welds.
Value of Proper Welding Strategies
Carrying out appropriate welding strategies is click to investigate paramount in guaranteeing the architectural integrity and top quality of bonded joints, building on the structure of effective porosity avoidance steps. Welding strategies directly impact the general toughness and longevity of the welded structure. One essential aspect of appropriate welding strategies is maintaining the proper heat input. Excessive warm can lead to boosted porosity due to the entrapment of gases in the weld swimming pool. Conversely, not enough heat may result in incomplete fusion, creating prospective powerlessness in the joint. Furthermore, making use of the suitable welding criteria, such as voltage, current, and take a trip speed, is important for achieving audio welds with marginal porosity.
Additionally, the option of welding procedure, whether it be MIG, TIG, or stick welding, ought to straighten with the particular requirements of the job to make sure optimum outcomes. Proper cleaning and preparation of the base metal, in addition to choosing the ideal filler product, are additionally important parts of proficient welding methods. By sticking to these best techniques, welders can reduce the risk of porosity formation and produce top quality, structurally sound welds.
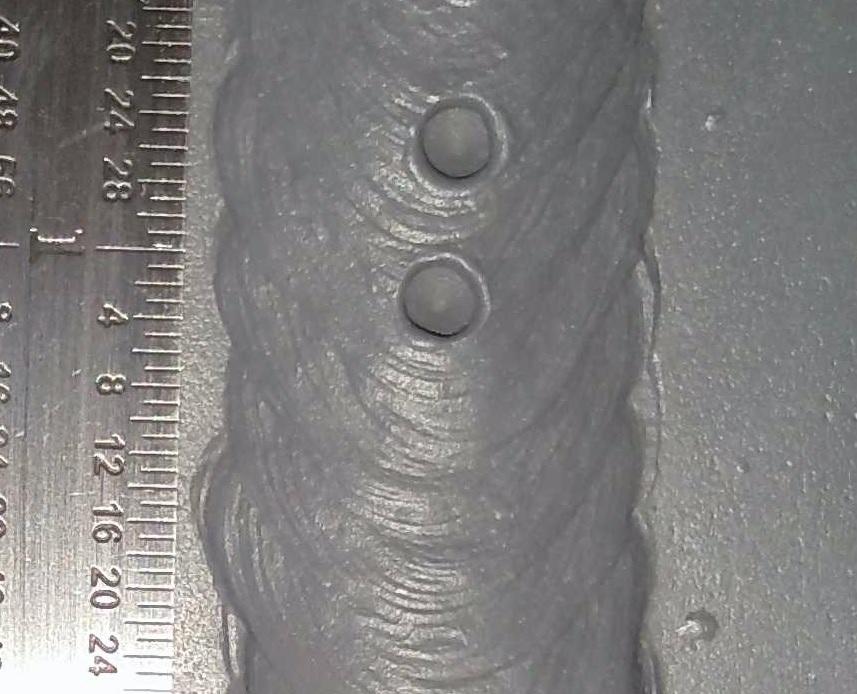
Evaluating and Quality Assurance Measures
Checking procedures are important to spot and prevent porosity in welding, ensuring the toughness and toughness of the final product. Non-destructive screening approaches such as ultrasonic testing, radiographic testing, and aesthetic examination are generally used to determine prospective defects like porosity.
Carrying out pre-weld and post-weld assessments is additionally critical in maintaining quality assurance requirements. Pre-weld assessments include validating the materials, equipment setups, and cleanliness of the workplace to stop contamination. Post-weld evaluations, on the various other hand, evaluate the last weld for any flaws, including porosity, and verify that it fulfills defined requirements. Carrying out a detailed quality assurance plan that includes comprehensive testing treatments and inspections is critical to minimizing porosity issues and guaranteeing the total quality of welded joints.
Final Thought
Finally, porosity in welding my blog can be an usual concern that influences the top quality of welds. By identifying the usual sources of porosity and applying finest techniques for prevention, such as appropriate welding methods and testing measures, welders can guarantee excellent quality and trusted welds. It is vital to focus on avoidance approaches to decrease the event of porosity and keep the honesty of bonded structures.